Borssele nuclear power plant
Borssele nuclear power plant was built on the basis of a simple, safe, robust design from the early 1960s. The German technology and the quality of the materials used in the plant enhanced the safety of the basic design.
The plant commenced operations in 1973. Every ten years, the state of the art in nuclear power plant design is explored, to establish what safety improvements can be made. In 1983, 1993 and 2003 the safety of the plant was evaluated, and improvements were made. The modifications made in 1986, 1997 and 2006 have retroactively enhanced the safety level of the plant’s design. The plant was already safe when it was commissioned in 1973 (10-3), and has since been made a thousand times safer (10-6).
A pressurised water reactor like the one at Borssele is an inherently safe design. The physical features of the reactor ensure that the fission process automatically stabilises in the event that parameters deviate too much from the norm. When the reactor power is too high, the temperature in the reactor rises which, in accordance with the laws of physics, causes the rate of fission to drop.
This decreases the power level, causing the temperature to drop.
No technical intervention is required. Briefly, this is because the physical properties of the water and uranium are such that the nuclear fission rate drops as the temperature rises. This is known as an inherent safety feature. The nuclear fission process is therefore highly stable and easy to control. This keeps operations simple, reducing the likelihood of disruption.
As long as the core remains submerged in water, damage that could lead to dangerous situations cannot occur. Water is always available for cooling and shielding, thanks to the numerous (redundant) systems and buffers discussed later on.
Watch this video of the nuclear fission process:
The reactor power is controlled by adding neutron-absorbing boron to the water in the reactor. Changing the concentration is a slow process. Rapid changes in reactor power are realised using the control rods [2] that hang in the top of the reactor [1]. They are operated by staff in the control room. When the control rods are lowered into the reactor, they absorb neutrons, thus reducing reactor power.
The control rods are held in place above the core by highly sensitive electromagnets, which release the rods when they receive the command to do so, or when parameters deviate from the norm.
As soon as the ‘hands’ release the rods, gravity ensures that they fall into the core. The neutrons are absorbed, and fission stops immediately.
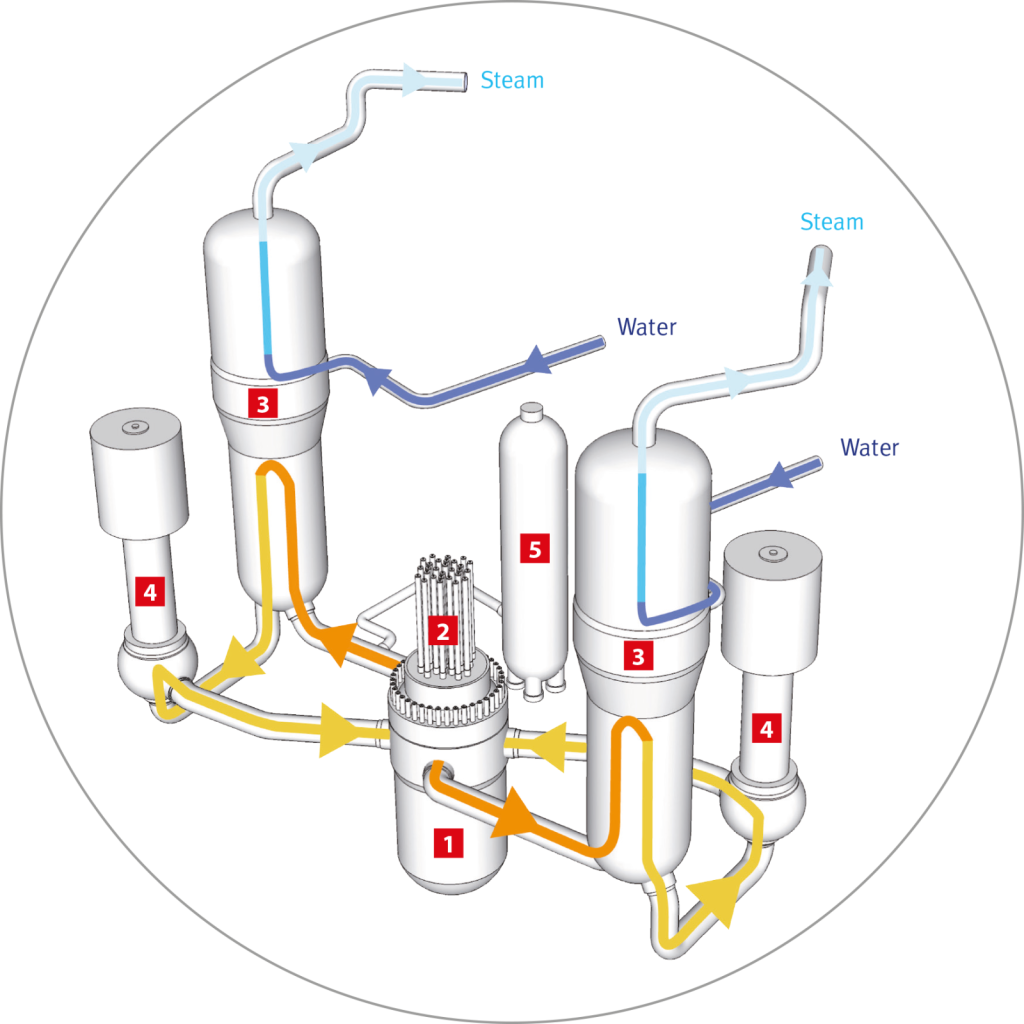
Nuclear fission occurs in the reactor [1]
This is controlled using the control rods [2].
Coolant ensures that heat is transported to the steam generator [3]. The coolant is returned to the reactor by the main coolant pump [4].
The coolant is under high pressure, so it cannot reach boiling point. Pressure deviations are levelled out by the pressuriser [5], which is similar to the expansion vessel in your central heating system.
Safely shielded by steel and concrete, the core [1] lies at the heart of our plant.
Here, heat is produced by the splitting of uranium or plutonium atoms – the reactor fuel.
The heat is absorbed by water in the primary (nuclear) circuit, which circulates through the reactor vessel [1] under high pressure. The heat is used to produce steam in the secondary (non-nuclear) circuit, in the steam generator [3]. The steam drives a turbine [6] on an axle that drives a generator [7]. The power generated is fed into the electricity grid. The steam condenses back to water in a condenser [8]. It is cooled using cold surface water from the Western Scheldt river [9], which is pumped through the condensers.
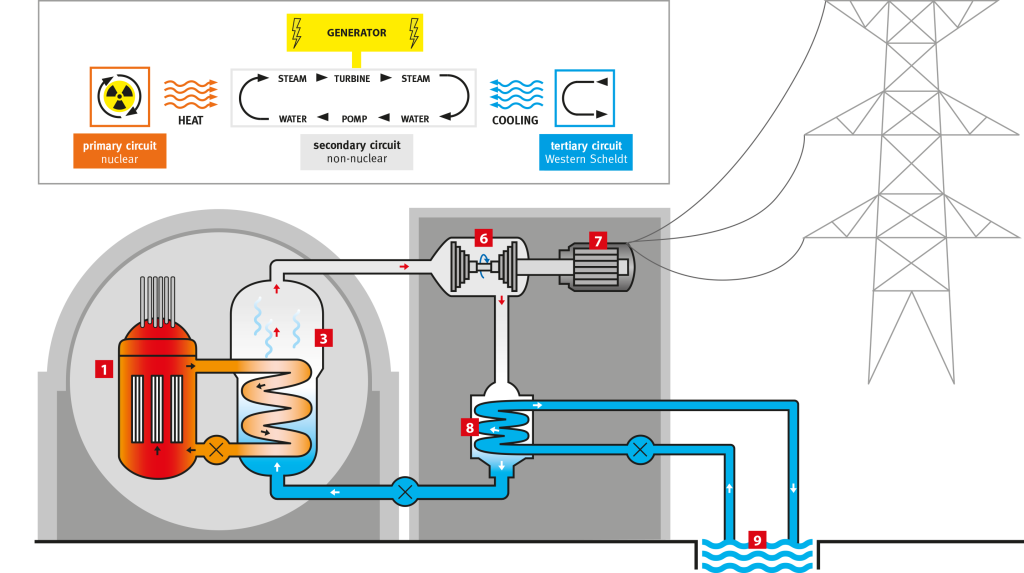
Watch this video of the production process:
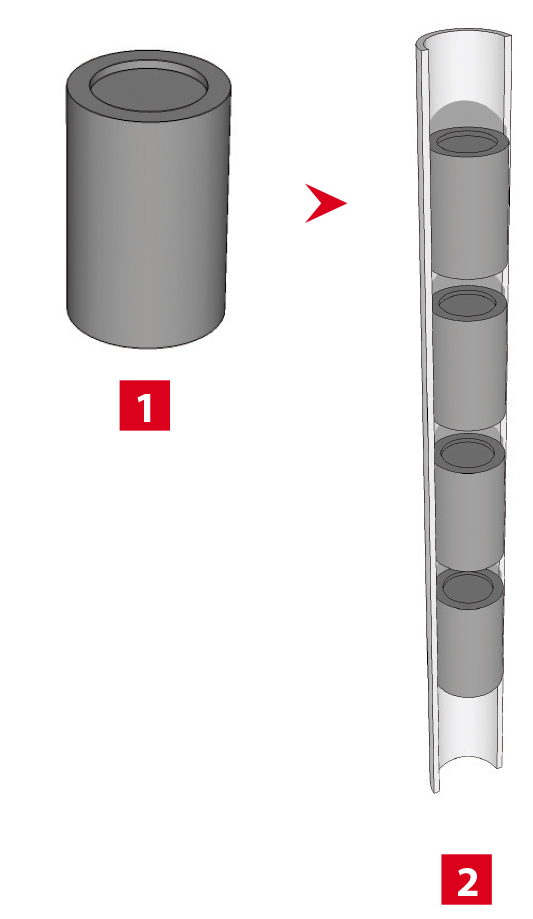
The nuclear plant has five safety barriers that protect people and the environment from radioactive incidents. The design of the plant is focused entirely on keeping radioactivity within its safety barriers under all process conditions.
Barrier 1: Fuel pellet [1]
The fuel pellet, sintered like porcelain, is the first barrier. Some 90% of the radioactivity remains sealed in the matrix of the fuel (uranium oxide). Only the highly volatile substances (noble gases, iodine, caesium) escape from the fuel pellet.
Barrier 2: Fuel rod [2]
The fuel pellets are stacked in a hermetically sealed, gas- and watertight zirconium tube. This fuel rod retains most of the volatile radioactive substances.
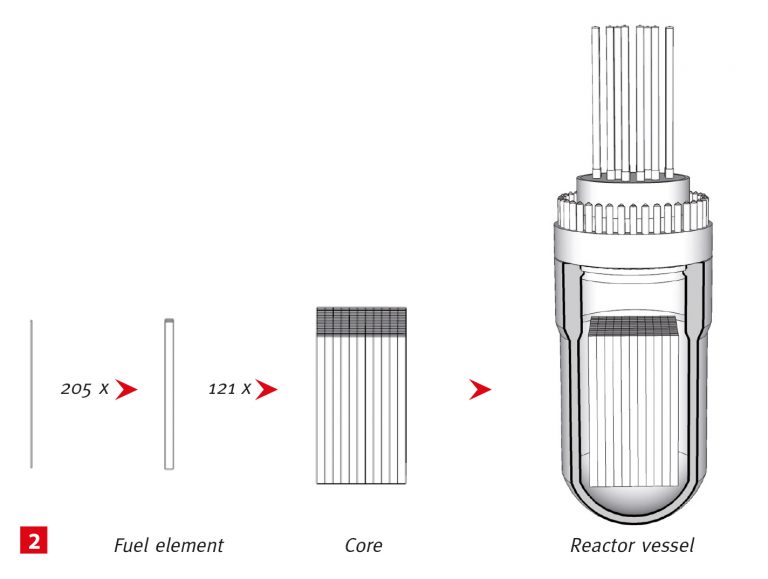
The core consists of fuel pellets sealed in fuel rods. A bundle of 205 fuel rods combine to a single fuel element. The reactor contains 121 of these elements. The core is contained in the primary system, a closed circuit of thick steel pipes, tubes, pumps and pressure vessels. The primary system is housed in bunkers inside the containment building, an airtight steel sphere. All nuclear systems are housed in a concrete structure whose most striking feature is the dome. It is not possible to break through all five barriers in a single coordinated action, which would be necessary to cause a nuclear discharge.

Barrier 3: Primary system [3]
The primary system is a closed circuit through which coolant (conditioned water) is pumped. The water, at approx. 320°C, is pressurised to 155 bars to prevent boiling, hence the name ‘pressurised water reactor’. The primary system (reactor vessel, pipelines, steam generators) is made of highly overdimensioned steel parts (several centimetres thick) of the highest quality. Radioactive substances cannot escape.
The primary system is housed in concrete bunkers. The concrete provides radiological protection during operations, and protects the primary system from internal or external threats.
Barrier 4: Containment structure [4]
The primary system is contained inside a steel sphere several centimetres thick, which ensures that radiation cannot escape if an incident occurs. The sphere is a strong airtight structure which can withstand internal gas and steam explosions. This prevents emissions from the primary system to the environment in the event of an accident.
Barrier 5: Reactor building [5]
All systems are contained inside the reactor building, which is instantly recognisable thanks to the familiar concrete dome. The building is the final physical barrier between the primary system and the outside world. The concrete structure is also the first barrier against external threats.
The nuclear plant’s ventilation shaft is often incorrectly referred to as a stack. It is through this shaft that the treated (filtered) air is vented to the external environment.
The air in the containment structure is underpressurised so that, in the event of a leak, air will always flow from the outside to the inside. The underpressure is constantly monitored.
An air treatment system maintains the underpressure and vents any excess (filtered) internal air through the ventilation shaft. This air is constantly checked for radioactivity.
When moving from one chamber to another, staff have to pass through an airlock. The chambers around the primary system (with the greatest underpressure) are hermetically sealed and inaccessible during normal operations. This prevents any radioactive gases or contaminants from escaping the plant unnoticed.
In the containment structure (closed steel sphere) at Borssele is a system that immediately converts into water any hydrogen that might develop. The system is passive, and requires no power or controls. It therefore works under all conditions. A catalyst (platinum) in the recombiners ensures a controlled chemical reaction, to rule out the danger of explosions.
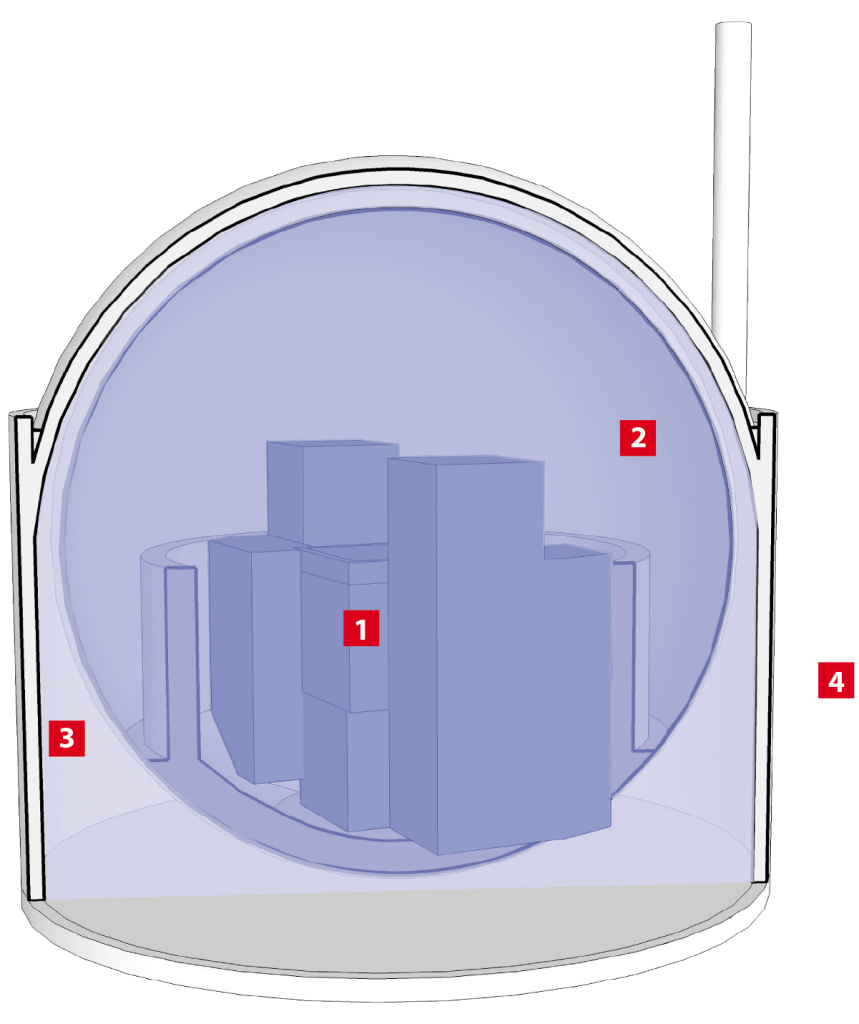
Pressure stages
[1] The greatest underpressure is in the area immediately surrounding the primary system.
[2] The other areas inside the steel sphere have slightly less underpressure.
[3] The space between the concrete dome and the steel sphere has less still.
[4] Ambient pressure.
Whether a nuclear power plant is in operation or has been shut down for maintenance, the fuel in a pressurised water reactor must always remain submerged, in order to remove the residual heat that the fuel produces due to radioactive decay, and to provide protection from radiation. As long as the core is covered with water, the situation can be controlled.
The plant has several independent systems and water supplies which ensure that the core remains covered with water in all circumstances. The plant also has systems that guarantee that the heat from the core can be discharged to a heat sink in all circumstances. These systems complement or substitute each other.
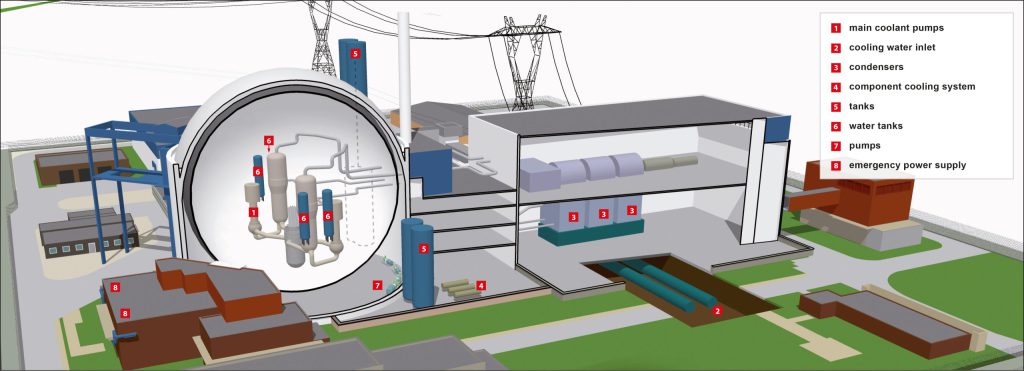
The nuclear plant has two main coolant pumps [1]. These pumps circulate coolant through the primary system while the plant is in operation. If both pumps fail, the reactor automatically shuts down and a process of natural circulation commences, with sufficient capacity to remove the decay heat from the core: without pumps, without technical intervention, simply on the basis of the laws of physics. This is the second major inherent safety feature of the reactor design at Borssele.
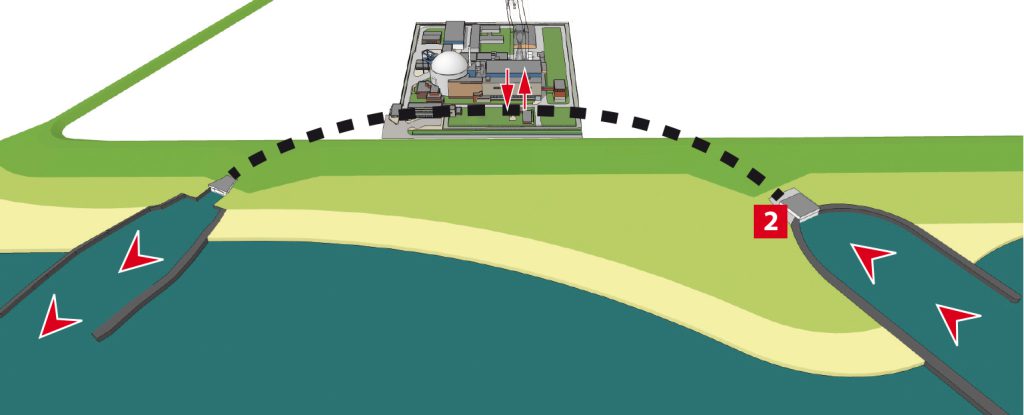
During normal operation and maintenance:
When the nuclear plant is generating electricity, the steam cycle is cooled using water from the Western Scheldt river, which is pumped in via the cooling water inlet [2].
Cooling occurs in the condensers [3], in which cold surface water ensures that the steam is condensed back into water, after which the steam cycle begins again. This cooling circuit is in fact part of the electricity production system, not the safety system.
When the power plant is not in operation, the core still has to be cooled so that residual heat is removed. Though the chain reaction has stopped, radioactive decay means the core continues to produce heat. The main coolant discharges this heat via the component cooling system [4] to redundant cooling water pipes containing water from the Western Scheldt. This cooling chain, consisting of three circuits separated by heat exchangers, has double pipelines to remove the decay heat from the reactor and discharge it to the Western Scheldt during normal operations, or when there is a technical fault. The two redundant trains therefore ensure that heat can be removed from the core.
For the unlikely event that water cannot be taken from the Western Scheldt, in 1997 EPZ installed a back-up system that uses eight deep wells that supply brackish groundwater.
Powerful underground pumps pump up brackish groundwater to remove the decay heat.
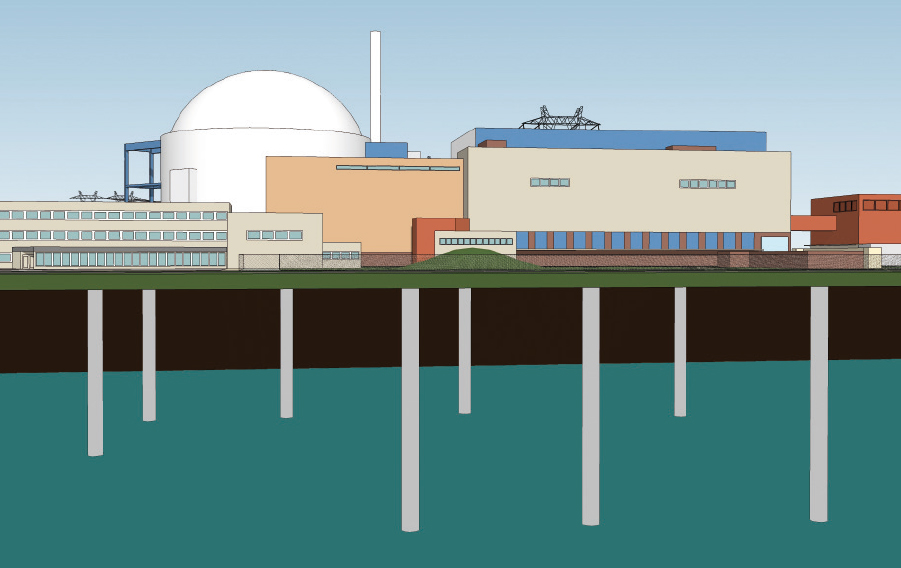
During cooling water leakage:
These tanks [5] top up the water if there is a leak in the primary circuit. The water is used to keep the core submerged. The water reserve is 700 m3, which can be supplied in two ways: under high pressure (110 bar) with a small throughput, or under low pressure (8 bar) with a high throughput, depending on the amount needed (high throughput for a major leak, low throughput for a small leak). The tanks were part of the original design, and have been present on the site since the plant commenced operations in 1973.
The sphere contains four water tanks (2 x 2) [6]. In the event of a loss of pressure in the primary system (which indicates there is a leak), the water automatically begins to flow once the pressure drops below 25 bar. The tanks contain a total of 86 m3 of water. This system also dates from 1973.
If both water supplies are exhausted, almost 780 m3 of water will have been pumped into the sphere. Pumps [7] were fitted beneath the sphere in 1973 to pump the water back to the reactor.
In 1984, after the nuclear accident in Harrisburg (USA, 1979), two extra bunkered water storage facilities (2 x 200 m3) were built at a short distance from the reactor building with their own emergency power supply [8], plus a further 400 m3 of water for independent water supply to the steam generators.
After the accident at Chernobyl, a great deal of attention was focused on the safety culture and operation of the process, and many improvements and safeguards were introduced.
Since Fukushima more consideration has been given to incidents on an unimaginably catastrophic scale. A scenario in which the entire Dutch infrastructure has been swept away and society has been so disrupted that external assistance is extremely difficult to provide has been considered:
- A new, additional 380 kV connection to the national electricity grid [9] has been installed.
- Extra cooling has been provided for the fuel storage basin.
- A facility for external cooling of the reactor vessel is to be introduced. In an emergency, water can be let into the empty space between the reactor vessel and the concrete containment structure [10].
- Extra equipment such as mobile pumps and generators have been purchased, which can be connected at several places in the plant.
- Larger, distributed diesel and water supplies that can be accessed in several ways have extended the period during which the nuclear power plant can manage without external assistance to fourteen days.
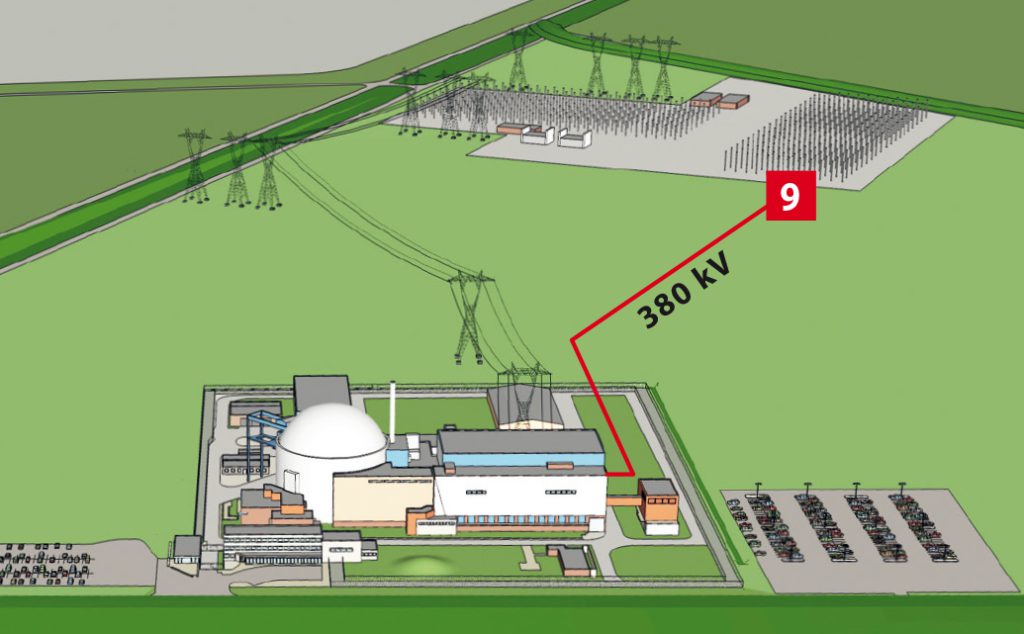
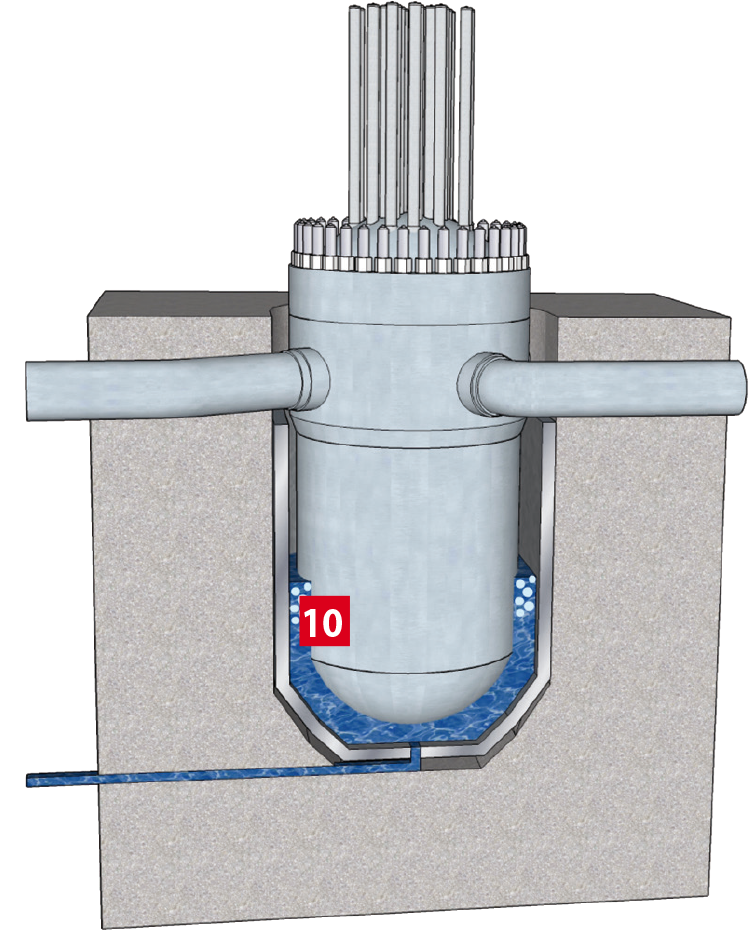
The nuclear plant not only produces electricity, it also uses electricity to control the plant. To ensure that the core remains covered with water at all times and that the decay heat is discharged, active components like pumps are needed, and they are powered by electricity. That is why the plant has been equipped with numerous (redundant) emergency power systems.
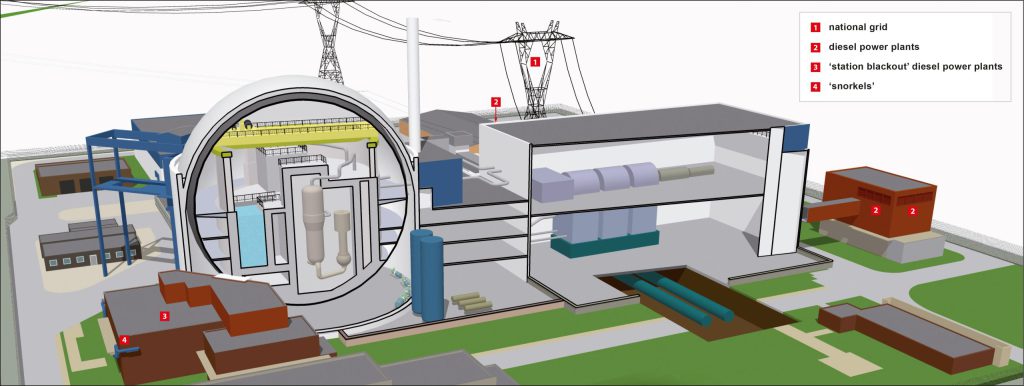
The nuclear plant consumes power from the national grid [1]. Since this power supply can fail, multiple connections have been installed. High-voltage pylons connect the plant with the public 150 kV electricity grid. Underground cables connect it to the 380 kV national interconnected grid. So electricity can be obtained from two different national grids.
There are three identical 5 MW diesel power plants [2] around the nuclear power plant. Each of them is highly overdimensioned and can independently supply the electricity needed to discharge residual heat. The diesel power plants in the original design were replaced in 1997 by larger ones housed in different buildings. A review of these plants was launched in 2017.
In 1986, two extra ‘station blackout’ diesel power plants [3] were built in bunkers. Each of these 1 MW plants can keep the nuclear plant in a safe, controlled state. In 2006 the flood defences were increased from 7.3 metres above NAP (Amsterdam Ordnance Datum) by fitting ‘snorkels’ [4] to the air inlet to a height of 9.8 metres above NAP.
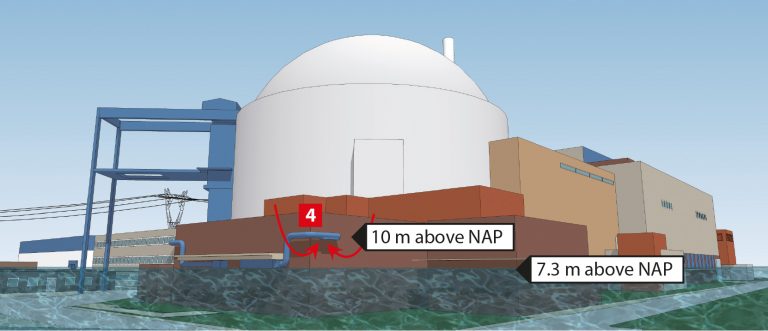
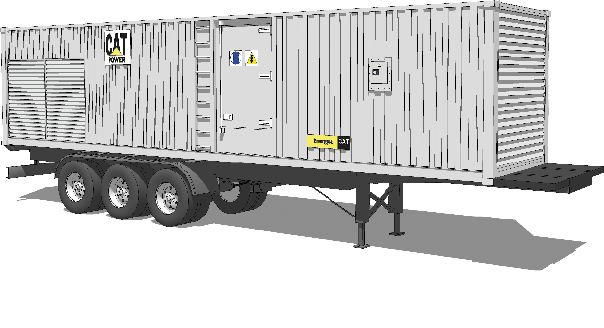
EPZ also has a mobile 1 MW diesel unit which serves as an additional emergency power supply for operating the plant, and several mobile units for operating smaller auxiliary systems.
The nuclear plant always shuts down safely and automatically if there is an incident. If the control room (and operator team) is no longer available, the shutdown can be managed from an auxiliary control room (built in 1997). A second team of operators monitor the automatic controls and ensure that everything is safe. They can intervene if necessary.
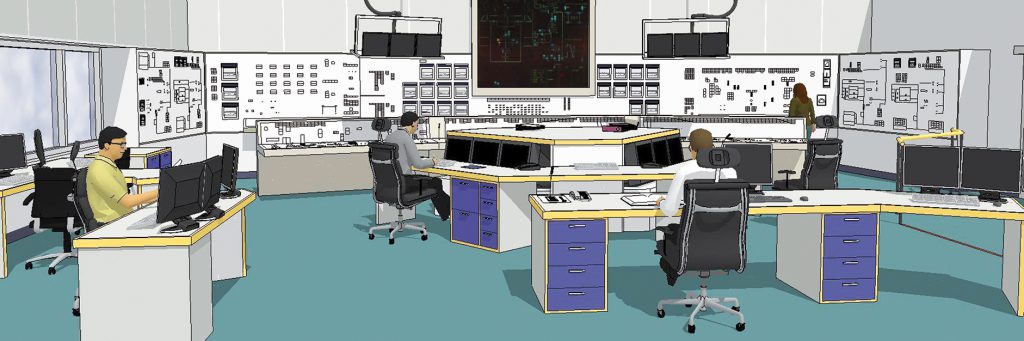